Why EWG? (itโs just about awesome turbo noises)
We hear this alot as the Mazdaspeed platform continues to grow and the 450-500whp build becomes the status quo. Following up the EWG Housing Design & Details Blog about the new CorkSport EWG Housing, we want to share some testing data and differences we saw between an IWG (internal wastegate) and EWG (external wastegate) setups.
Details about design, flow, placement, data, and feedback from our CST4 EWG Beta Tester.
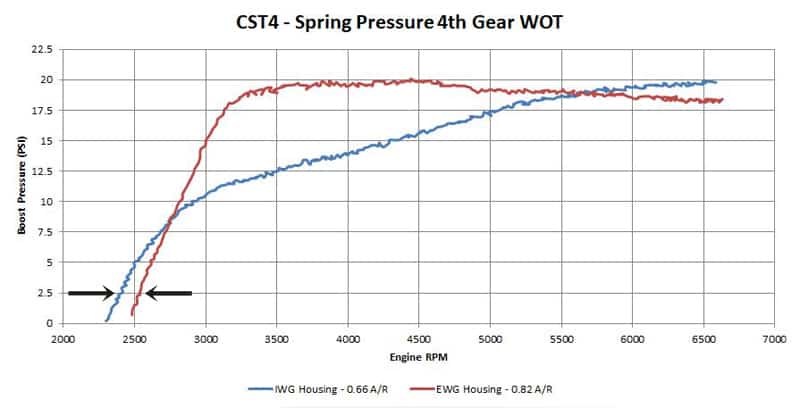
Letโs jump right in! First up is a spring pressure comparison between the IWG and EWG housing on a CST4 turbocharger. Letโs first define what โspringโ pressure is: this is the resulting boost pressure with 0 added wastegate duty cycle. AKA we are not trying to add boost pressure.
Immediately you can see some very obvious differences. The IWG setup has a taper up boost curve that could be considered boost creep. Some boost creep is ok, but an excessive amount may reach the capacity of the fuel system or other systems in the vehicle. In this setup that is not the case, but it does show that the IWG is at its limits for boost control.
With the EWG setup you see a much different curve. The boost builds a few hundred RPM later (due to the larger 0.82 A/R) then climbs right to the spring pressure and then settles to a consistent plateau; very predictable and controllable.
Now letโs look at the design to better understand why. On the left is the EWG turbine housing with a 0.82 A/R and on the right is the IWG turbine housing also with a 0.82 A/R (we donโt want the A/R to be a factor in this review).
The EWG housing has a very efficient flow path for the exhaust gas to reach the EWG control valve along with a much larger path to flow. Both of these features provide excellent flow and thus control of boost pressure.
The IWG housing uses a side port in the turbine scroll to exhaust gas. In this setup, the exhaust gas must make an abrupt turn and pass through a much smaller port. Both of these issues reduce boost control.
Here is a diagram showing placement of an EWG in the exhaust pre-turbine. Granted we are comparing a EWG and IWG, but the concept of flow is the same.
Exhaust gases will always take the path of least resistance and if the turbine wheel is the easier path than the wastegate then boost control will be more difficult.
(Right) External Wastegate Setup | Optimized Setup
Click to Expand
This graph was shown in the last blog, but we want to show it again so you can directly compare it to the data graph below.
Below is the boost curves for the CST5 in both IWG and EWG setup. Alone each graph actually looks really good, but when overlaid you can see some interesting differences.
IWG vs. EWG on the CST5
The purple IWG graph has a crisp spool and then flat-lines at approximately 30psi with a slight fall off at 6500rpm. The CST5 IWG setup does control boost really well, but holding the turbo back at spool up and not over-boosting or spiking was a small challenge. An abrupt boost curve like this can make the car somewhat difficult to drive because the torque โhitsโ very hard and you lose traction.
The EWG setup was a bit more controllable. ย Not only did the CST5 Mazdaspeed turbo spool a bit sooner, but we were able to better control the spool up boost curve so we could create a torque curve that was more friendly to the FWD traction. ย This makes the car more fun to drive. Looking at the higher RPM range we were also able to hold boost more consistently to 7500rpm.
We hope you guys and gals are as excited for the EWG options for the CST4, CST5 and CST6. ย They really are an awesome setup for any driving style and power goal. ย
Thanks for tuning in with CorkSport Performance.
-Barett @ CorkSport