A few months ago we broke down the complicated design of the exhaust manifold found on the 2014-2018 Mazda 3 & 6 2.5L SkyActiv. Mazda put extensive R&D into the design and packaging of the OEM header to optimize the exhaust gas pulses and overlap.
In this blog we are going to explain some of the design features in the CorkSport 4-2-1 header and why those features are important.
Below is a diagram showing the primary, secondary and collector routing of the OE header.
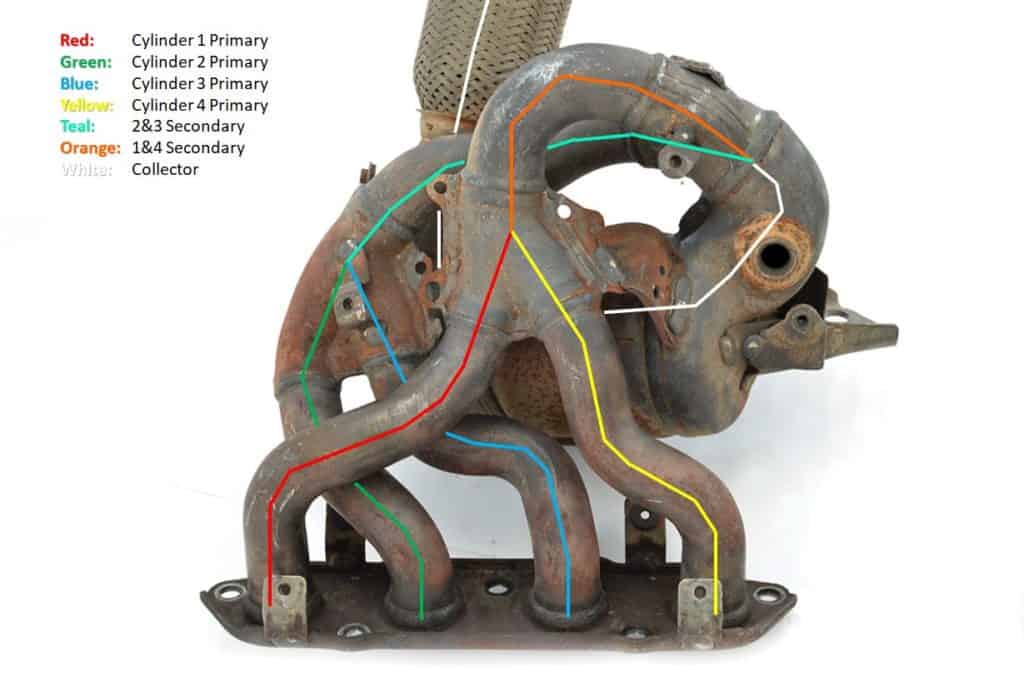
When designing a performance header we have to ask ourselves, โwhat is the goal with this performance part?โ and then fulfill that goal. With the performance header for the 2.5L SkyActiv our goal was to increase mid-range torque, retain good fitment and user installation, and improve the sound output of the exhaust system.
Immediately youโll notice a significant difference in the design of the OEM header and the CorkSport Header. There are three major differences:
- Primary, secondary, and collector diameters have been increased to promote better exhaust gas flow.
- Primary and secondary runner lengths have been increased to optimize power/torque lower in the RPM range.
- The design is two-piece to drastically improve the installation process.
The primary runners (these are the runners that mate directly to the engine) have been increased in diameter from 1.55โ to 1.75โ and the secondary runners (these are the runners that combine only two cylinders before the collector) have been increased in diameter from 1.87โ to 2.00โ. Both of these changes improve peak flow per cylinder throughout the RPM range. Lastly, the collector has been increased from 2.00โ to 3.00โ to be paired with the CorkSport 60.5mm or 80mm Cat-Back Exhaust Systems.
Hereโs where things got a bit tricky. Increasing the length of the primary and secondary runners forced us to be a bit creative in routing all the piping. In order to achieve the primary runner length we wanted, we had to route the piping upward first (as you can see below) then back down between the engine and firewall. The results were better than we expected with a โMedusaโ style header peeking out of the engine bay and the lengths we wanted.
It makes us grin every time we pop the hood open, we hope you love it as much as we do.
However, the complicated CorkSport design did create a new problem. Installation! We always try to create a performance part that can be installed by the average enthusiast in their garage and this was no exception. In a one-piece design, the header was nearly impossible to install. We went to the drawing board and realized that separating the upper and lower halves of the header was the best option.
We considered a conventional flange, gasket and hardware setup, but realized it to was far too complex in the close quarters behind the engine. We then moved to a v-band connection that proved to be the best setup for installation, weight, and sealing ability.
That wraps up the design, next weโll breakdown the testing and results! Let us know if you have any questions or thoughts down below.
-Barett @ CorkSport